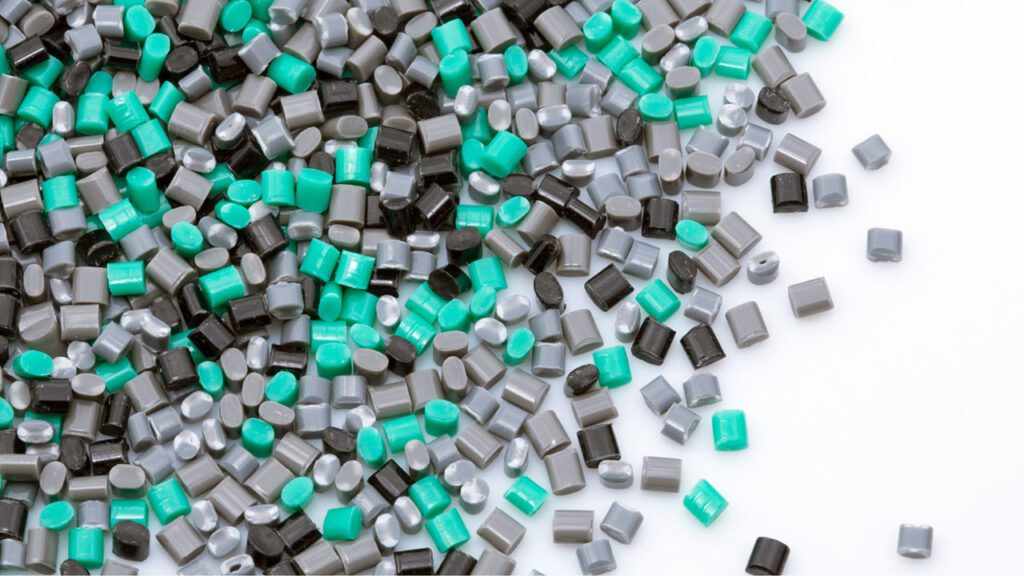
Thermosetting plastics are an important class of materials that undergo a chemical change when heated, becoming rigid and solid. Unlike thermoplastics which soften when heated, thermosetting plastics harden permanently once cured and cannot be reshaped by heating. Some key types of thermosetting plastics are discussed below.
Phenol Formaldehyde Resins
One of the earliest developed and still widely used Thermosetting Plastics is phenol formaldehyde resin, also known as phenolic resin. It is produced by the condensation reaction of phenol or substituted phenol with formaldehyde. Phenolic resins exhibit heat resistance and good mechanical properties. They also have very good electrical insulation properties. As a result, they find applications as molding compounds for electrical equipment and insulators. Given their heat resistance, phenolic resins are also used to manufacture stove parts, iron cladding and as ablative materials in shuttle vehicles.
Epoxy Resins
Epoxy resins are produced by reacting epichlorohydrin with bisphenol-A. They possess excellent heat resistance, adhesion properties and mechanical strength even after curing. Epoxy resins are commonly used for electrical insulation, as coatings and adhesives. They are also used to make composite materials such as fiber-reinforced plastic due to their ability to wet fibers and bond strongly to them. Epoxy is a preferred material for making printed circuit boards due to its dimensional stability at high temperatures.
Polyesters
Unsaturated polyester resins are produced by polycondensation of an unsaturated dicarboxylic acid such as maleic acid with a polyhydric alcohol such as propylene glycol. They cure rapidly when exposed to catalysts, heat or ultraviolet radiation. Polyester resins are notable for their high strength, poor moisture absorption and ability to bond strongly with fiberglass and other materials. As a result, they serve as matrix resins for glass-reinforced plastics used in applications like boat hulls, water tanks, swimming pools and bathtubs where strength and corrosion resistance are required.
Applications Across Industries
The versatility and superior properties of thermosetting plastics enable their usage in many industries.
Electronics: Epoxy resins are widely used in electronic devices from PCB laminates and wiring to encapsulation of semiconductor chips to provide electrical and structural integrity at high operating temperatures.
Construction: Polyester, vinyl ester and epoxy resins reinforced with fiberglass are used to manufacture strong, lightweight and corrosion-resistant products like pipes, storage tanks and bathroom fittings.
Automotive: Phenolic resins are utilized in braking systems parts while epoxies are preferred for gear casings. Polyesters are ideal for layers and parts requiring dent and corrosion resistance.
Aerospace: Epoxy matrix composites reinforced with carbon/glass fibers are most common due to their high strength to weight ratios. They are used in structural parts, rocket casings and radomes.
Appliances: Stove parts, wash basins, water heaters frequently employ thermosetting plastics for their self-extinguishing properties and ability to withstand high heat and chemical exposure.
Electrical Insulation: Besides transformer coils and switch gear components, thermosetting plastics are molded into insulation parts that withstand electrical, chemical and mechanical stress over long operating periods.
Adhesives and Coatings: Epoxy and polyurethane adhesives along with polyester and epoxy based paints and coatings have enabled product assembly and corrosion protection in multiple industries.
Manufacturing Processes
Thermosetting plastics can be shaped by various manufacturing techniques suitable for the particular type of resin:
- Compression molding: Used for large auto and appliance components requiring high mechanical strength. Thermosetting granules are compression molded in preheated molds.
- Injection molding: Popular for intricate electrical switchgear parts and small consumer items. Melted resin is injected into molds under high pressure.
- Transfer molding: Epoxy molding compounds are melted and injected at low pressures into molds placed on a movable table. Used for IC packaging.
- Pultrusion: Continuous process to produce composite profiles by pulling roving material through a thermoset resin bath and die curing. Common for structural plastics.
- Filament winding: Continuous reinforcement rovings are wrapped helically on a rotating mandrel pre-impregnated with resin. Useful method for pipes and pressure vessels.
Future Prospects
As demand rises across industries for materials combining high strength, stiffness, heat resistance and dimensional stability, thermosetting plastics are positioned for steady future growth. Ongoing innovations will further expand their applications in aerospace, transportation, construction and electricity infrastructure. With their versatile properties and processing ease, thermosetting plastics will remain indispensable engineering materials.
Get More Insights - Thermosetting Plastics
Get This Report in Japanese Language - 熱硬化性プラスチック
Get This Report in Korean Language - 열경화성 플라스틱
About Author:
Vaagisha brings over three years of expertise as a content editor in the market research domain. Originally a creative writer, she discovered her passion for editing, combining her flair for writing with a meticulous eye for detail. Her ability to craft and refine compelling content makes her an invaluable asset in delivering polished and engaging write-ups.
(LinkedIn: https://www.linkedin.com/in/vaagisha-singh-8080b91)
Thermosetting Plastics, Heat-Resistant Polymers, Phenol Formaldehyde, Urea Formaldehyde, Coherent Market Insights.
Write a comment ...